Rail Car Electrical Enclosure
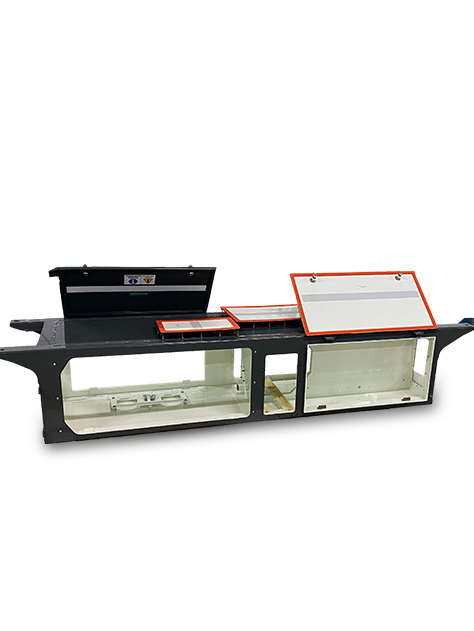
After evaluating several premier fabricators, DAWSON was chosen to manufacture custom electrical enclosures that house propulsion equipment used in light rail vehicles (LRVs) that transport passengers. DAWSON was successful in meeting the established design, budget, and volume that the project required.
DAWSON manufactures, paints, and assembles these units.
With stringent requirements in hand, DAWSON was able to secure a contract with its customer to manufacture, assemble, and paint 52 large enclosures and 26 smaller enclosures. These enclosures house propulsion systems that power light rail vehicles such as streetcars and trams.
To construct the enclosures, materials are laser/turret punched and brake-formed before heading to be machined and welded. The formed pieces are then primed with a PPG Powercron cationic epoxy electrocoat and finished with a Tiger Drylac Series 49 Polyester TGIC weather-resistant powder topcoat. The pieces are then assembled exclusively by rivets – using over 3,000 per unit.
Finishes:
Materials: